Совершенствование технологии замены дефектных участков магистральных нефте- и газопроводов с использованием данных лазерного сканирования
Текущее состояние. При эксплуатации магистральных трубопроводов в теле трубы и на ее поверхности возникает множество дефектов. Основным методом устранения таких дефектов является вырезка дефектного участка и приварка на его место нового бездефектного. Процесс вырезки осложняется возможным резким смещением концов трубопровода, находящихся по обеим сторонам от места разрезания, что опасно для жизни рабочих и может приводить к поломке режущего оборудования. Также для приварки нового участка необходимо центрировать концы трубопровода до достижения ими положения соосности, для чего применяются тяжелые, труднотранспортируемые трубоукладчики, которые позволяют центрировать концы трубопровода только путем их подъема. Обеспечение возможности такого центрирования зачастую требует дополнительного откапывания ремонтируемого трубопровода. Также ввиду больших габаритов трубоукладчиков требуется оплата разрешений на их транспортировку. При этом требуется разборка трубоукладчиков перед транспортировкой и сборка их перед проведением ремонтных работ, что влечет за собой дополнительные затраты времени и труда рабочих. При этом предлагаемые специалистами способы ремонта трубопроводов либо не обеспечивают достаточного уровня производственной безопасности, либо являются технологически и экономически неэффективными.
Решаемая научная проблема. Предлагаемый способ ремонта заключается в откапывании дефектного участка трубопровода, определении его пространственного положения в ремонтном котловане путем лазерного сканирования, обработке данных лазерного сканирования, проведении расчета сил реакций, возникающих в гидроцилиндрах предлагаемых устройств фиксирования и центрирования концов трубопровода при резком смещении концов в результате разрезания трубопровода, расчета усилий, необходимых для центрирования концов трубопровода с помощью предлагаемых устройств, установке устройств на трубопровод, фиксировании положения его концов, вырезке дефектного участка, центрировании концов с торцами нового бездефектного участка, а также приварке нового участка.
Для разработки предлагаемого способа ремонта требуется решить следующие задачи:
- Разработать конструкцию устройства фиксирования и центрирования концов трубопровода на основе выявленных достоинств и недостатков предлагаемых в настоящее время устройств.
- Разработать метод оценки положения в пространстве изогнутой центральной оси трубопровода на основе его облака точек, полученного в результате лазерного сканирования.
- Разработать математическую модель для оценки нагрузок, которые будут воспринимать предлагаемые устройства в процессе их эксплуатации, а также усилий для центрирования концов трубопровода. При этом в качестве исходных данных для математической модели выступает уравнение изогнутой оси трубопровода, полученное по результатам лазерного сканирования.
- Разработать схему конструкции устройств фиксирования и центрирования концов трубопровода для устранения резкого смещения концов трубопровода при его разрезании и их дальнейшего центрирования перед приваркой нового участка.
- Провести экспериментальное исследование точности оценки сил реакций, возникающих в гидроцилиндрах устройств, и усилий центрирования концов трубопровода по предлагаемым математическим моделям на основе данных лазерного сканирования трубопровода.
- Осуществить проверку сходимости результатов расчета по предлагаемой математической модели с результатами конечно-элементного компьютерного моделирования.
Методы исследования. При разработке предлагаемых устройств фиксирования и центрирования концов трубопровода осуществлялся патентный поиск на предмет предложенных специалистами конструкций устройств, среди которых не было выявлено таких, которые бы полностью удовлетворяли требованиям производственной безопасности и обеспечивали технологическую эффективность процесса ремонтных работ.
Разработка математической модели усилий, возникающих в гидроцилиндрах предлагаемых устройств при резком смещении концов трубопровода, а также усилий, необходимых для их центрирования перед приваркой нового участка осуществлялась методом сил, заключающемся в перемножении эпюр изгибающих моментов, действующих на трубопровод в процессе ремонтных работ и расчете канонических коэффициентов системы линейных алгебраических уравнений.
При проведении экспериментальных исследований осуществлялся упругий изгиб исследуемого трубопровода наружным диаметром 51 мм, толщиной стенки 3 мм, длиной 1,6 м, выполненного из стали 09Г2С, путем жесткой заделки его одного конца и приложении усилия 400 Н со стороны другого конца электрическим прессом Testometric M350-5CT. Предварительно вдоль боковой образующей трубопровода осуществлялась наклейка крестовых маркеров для дальнейшего их фотографирования и построения кривой изгиба центральной оси трубопровода. Далее осуществлялось лазерное сканирование исследуемого трубопровода в состоянии его упругого изгиба лазерным сканером Hexagon RS6 Laser Scanner. После чего трубопровод фотографировали с помощью камеры высококачественной съемки Hasselblad H5D 200 MS.
Далее в программном обеспечении ТЕМА Motion осуществлялся анализ координат положения крестовых маркеров вдоль трубопровода. Полученные координаты так же аппроксимировались полиномом четвертой степени, отражающим действительное пространственное положение трубопровода.
Следующим шагом в программном обеспечении SpatialAnalyzer осуществлялась фильтрация полученного в результате лазерного сканирования облака точек, построение вертикальных плоскостей с шагом 5 см вдоль трубопровода, аппроксимация принадлежащих плоскостям точек облака уравнением эллипса и аппроксимацией центральных точек полученных эллипсов полиномом четвертого порядка. Полученный полином описывает положение изогнутой оси трубопровода в пространстве.
Разработанные математические модели также верифицировались путем компьютерного моделирования процесса ремонта трубопровода в программном комплексе ANSYS. Полученные результаты различаются менее чем на 5%, что говорит о достаточной точности предложенных математических моделей при оценке искомых параметров.
Детали исследования. Разработанная конструкция устройств фиксирования и центрирования позволяет зафиксировать положение самих устройств в пространстве за счет применения в их конструкции буровых анкеров, забуриваемых в грунт. Система захватов, оборудованных гидроцилиндрами позволяет надежно зафиксировать положение концов трубопровода перед разрезанием, а также центрировать его концы относительно друг друга.
Последовательность ремонтных работ с применением предлагаемых устройств представлена на рисунке 1.
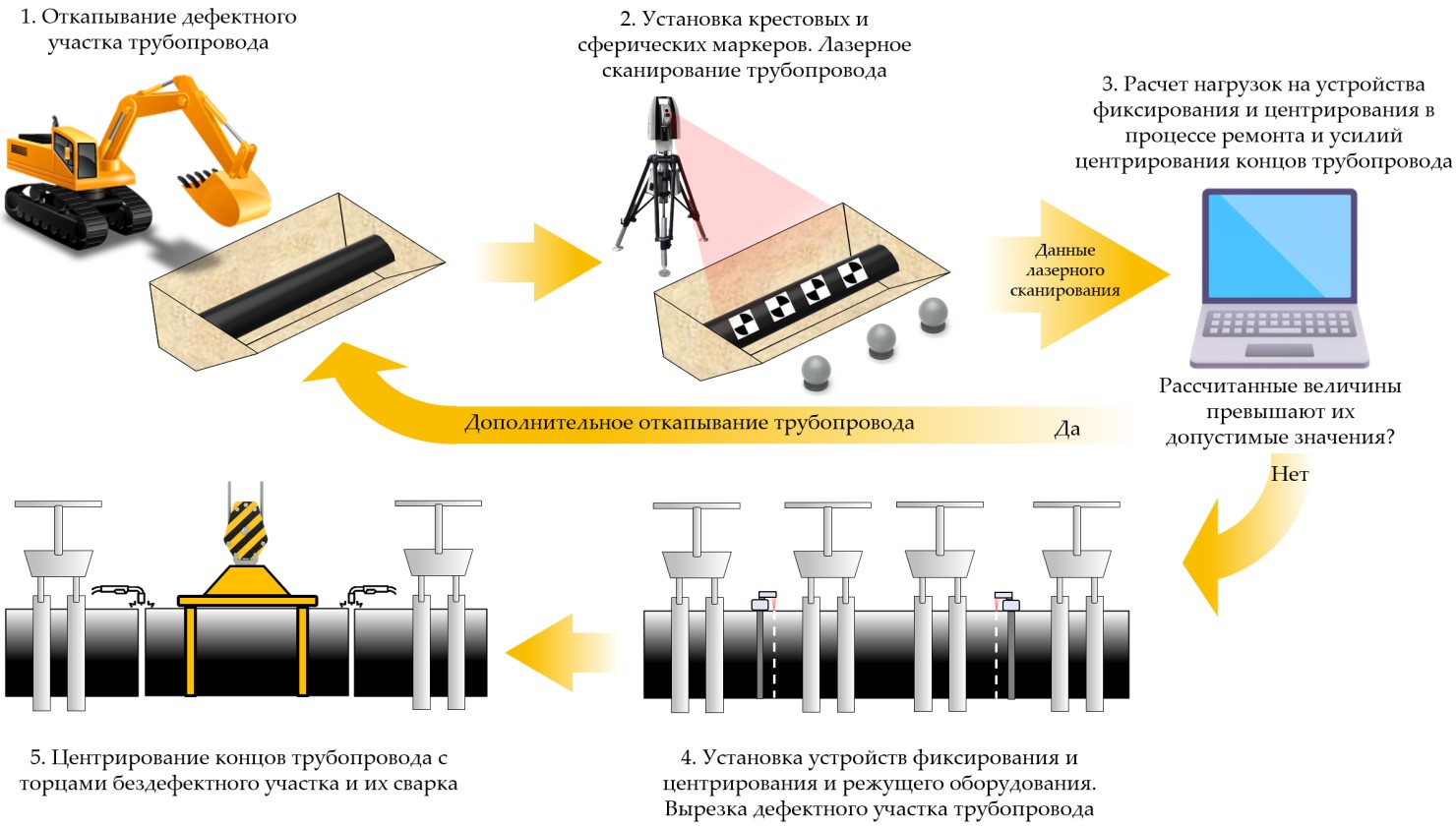
Рисунок 1 – Последовательность ремонтных работ с применением предлагаемых устройств
Задача разработки математических моделей решалась посредством расчета величин сил реакций, возникающих в гидроцилиндрах устройств при внезапном снятии статической нагрузки в месте разрезания трубопровода, в результате действия которой создается наблюдаемое высотно-плановое положение трубопровода в ремонтном котловане.
При проведении экспериментальных исследований осуществлялся упругий изгиб исследуемого трубопровода наружным диаметром 51 мм, толщиной стенки 3 мм, длиной 1,6 м, выполненного из стали 09Г2С, путем жесткой заделки его одного конца и приложении усилия 400 Н со стороны другого конца электрическим прессом Testometric M350-5CT. Предварительно вдоль боковой образующей трубопровода осуществлялась наклейка крестовых маркеров для дальнейшего их фотографирования и построения кривой изгиба центральной оси трубопровода. Далее осуществлялось лазерное сканирование исследуемого трубопровода в состоянии его упругого изгиба лазерным сканером Hexagon RS6 Laser Scanner. После чего трубопровод фотографировали с помощью камеры высококачественной съемки Hasselblad H5D 200 MS.
Далее в программном обеспечении ТЕМА Motion осуществлялся анализ координат положения крестовых маркеров вдоль трубопровода. Полученные координаты так же аппроксимировались полиномом четвертой степени, отражающим действительное пространственное положение трубопровода.
Следующим шагом в программном обеспечении SpatialAnalyzer осуществлялась фильтрация полученного в результате лазерного сканирования облака точек, построение вертикальных плоскостей с шагом 5 см вдоль трубопровода, аппроксимация принадлежащих плоскостям точек облака уравнением эллипса и аппроксимацией центральных точек полученных эллипсов полиномом четвертого порядка. Полученный полином описывает положение изогнутой оси трубопровода в пространстве.
При использовании двух полученных полиномов в расчетах по предложенной математической модели результаты различались на величину менее 5%, что говорит о достаточной точности оценки положения трубопровода в пространстве по результатам лазерного сканирования и реализации предложенного способа обработки данных сканирования.
Далее осуществлялся расчет усилий, возникающих в гидроцилиндрах устройств фиксирования и центрирования при резком смещении концов трубопровода в процессе его разрезания, а также усилий, необходимых для центрирования концов трубопровода, рассчитываемых по предлагаемым математическим моделям. В качестве исходных данных для расчета использовались уравнения полиномов изгиба, описывающих изгиб центральной оси трубопровода, полученных путем его лазерного сканирования и фотосъемки крестовых маркеров. Результаты расчетов для каждого из двух полиномов различаются менее чем на 5%, что свидетельствует о работоспособности предлагаемой технологии обработки данных лазерного сканирования для оценки пространственного положения трубопровода и проведения расчетов по разработанным математическим моделям.
Предлагаемые математические модели также верифицировались путем компьютерного моделирования процесса ремонта трубопровода в программном комплексе ANSYS.
По результатам расчета годовых эксплуатационных затрат на проведение ремонтов одним сервисным подразделением, занимающимся трубопроводной транспортировкой нефти и газа, было выявлено, что наибольший объем затрат производится ввиду применения в процессе ремонтных работ трубоукладчиков (оформление разрешения на провоз негабаритной техники, амортизация, затраты на топливо). Исходя из этого, применение предлагаемых устройств фиксирования и центрирования концов трубопровода взамен трубоукладчиков позволит существенно сократить объем эксплуатационных затрат, что свидетельствует об экономической эффективности применения предлагаемого способа ремонта.
Заключение. В результате проведенного исследования были сделаны следующие выводы:
1. Обоснованы недостатки существующих способов ремонта магистральных нефтегазопроводов с вырезкой дефектных участков.
2. Разработана и запатентована конструкция устройств фиксирования и центрирования концов трубопровода, позволяющая избежать резкого смещения концов трубопровода и обеспечить их центрирование перед приваркой нового участка без применения трубоукладчиков.
3. Разработана математическая модель для расчета сил реакции, возникающих в гидроцилиндрах фиксирующих и центрирующих устройств, усилий, необходимых для центрирования концов трубопровода, а также возникающих при этом напряжений в стенке трубопровода. Исходными данными для расчетов на основе математической модели являются данные о положении трубопровода в ремонтном котловане. Математическая модель рабочего обеспечит безопасную автоматическую работу устройств без присутствия персонала в траншее.
4. Обоснован выбор метода лазерного сканирования трубопровода для определения положения трубопровода в ремонтном котловане.
5. Разработан метод обработки облака точек трубопровода, полученного в результате лазерного сканирования. Метод позволяет получить полином, описывающий пространственное положение центральной оси трубопровода, исходя из его облака точек.
6. В результате лабораторного исследования установлено, что разработанный метод обработки облака точек сканируемого трубопровода позволяет получить полином, на основании которого можно с достаточной точностью произвести оценку (до 5%) параметров, рассчитанных по математической модели, по сравнению с методом фотографирования крестовых маркеров, наклеенных на боковую образующую трубопровода.
7. В результате моделирования процесса резки магистрального трубопровода и центрирования его концов методом конечно-элементного компьютерного моделирования достигнута достаточная сходимость (до 5 %) результатов моделирования с результатами расчетов по предложенной математической модели.
8. По результатам расчета годовых эксплуатационных затрат на производство ремонтных работ по применяемой в настоящее время технологии выявлено, что основные затраты (оформление разрешения на провоз негабаритной техники, амортизация, затраты на топливо) производятся ввиду применения трубоукладчиков. Предложенные в работе устройства позволяют значительно сократить эти статьи затрат и полностью исключить самую крупную из них – стоимость разрешения на перевозку негабаритной техники.
9. Разработанный метод ремонта магистральных нефтегазопроводов и математическая модель позволят повысить уровень промышленной безопасности процесса ремонта, а также его технологическую и экономическую эффективность.