Повышение эксплуатационной надёжности узлов и элементов самосвалов с учётом наименее надёжных элементов системы
Текущее состояние. В настоящее время в горной промышленности используются электросамосвалы Hitachi и другие большой мощности. Эти системы обладают аппаратами управления. Аппараты управления имеют достаточно высокую конструктивную сложность. В связи с этим эксплуатация таких технических систем нередко сопровождается значительным числом отказов составляющего их оборудования.
Решаемая научная проблема. Высокое качество, высокая эффективность, живучесть, безопасность, устойчивость, хорошая управляемость системы, в общем и целом, могут быть достигнуты при условии стабильной работы всех элементов системы. Все перечисленные свойства оборудования обеспечиваются за счет высокой надежности. В сложных технических системах, таких как карьерные электросамосвалы и другие установки с количеством подсистем узлов и деталей, достигающим нескольких сотен и тысяч, очень сложно описать их в виде блочно-функциональной декомпозиции и учесть взаимовлияние составляющих технической системы. Поэтому предложен подход, в первую очередь, определить надежность наиболее слабых, часто отказываемых узлов, на которые приходится основной поток отказов и повышать надежность всей системы именно с них.
Целью данной работы является моделирование и определение надёжности электрических аппаратов оборудования электросамосвалов с учетом наиболее отказываемых деталей для обоснования экономического выбора затрат на поддержание и повышение эксплуатационной надежности.
Для достижения поставленной цели необходимо:
1. Выполнить анализ важнейших показателей надежности компонентов электрических устройств карьерных самосвалов.
2. Предложить аналитические методы оценки показателей надежности компонентов электрических устройств карьерных самосвалов.
3. Разработать математическую модель отказов оборудования с дифференциацией обслуживаемого оборудования по повторному сроку службы, что позволит формировать гибкие графики технического обслуживания и ремонта. Реализация таких циклов позволит перейти от плановых ремонтов к системе ремонта в соответствии с фактическим ресурсом оборудования.
Методы исследования. Применен комплексный метод, включающий анализ и обобщение результатов ранее выполненных исследований надёжности систем аппаратов в горной промышленности. Авторами для получения достоверных показателей надёжности объекта пользовались двумя подходами. Подход № 1 заключается в таком отличие как высокая стоимость испытательных работ. Для такого способа характерно проведение специальных испытаний, определяющих надёжность объекта. Результатом данных испытаний является получение достоверных показателей надёжности объекта. Подход № 2 основывается на результатах работы объектов. Эти результаты получаются в ходе производственной эксплуатации этих объектов.
Детали исследования. Оптимизация ремонтно-обслуживающих циклов электрооборудования для горных машин выявило ряд задач исследовательского характера, таких как группировка электрооборудования по сходному остаточному ресурсу, которая позволяет сформировать эффективные циклы ремонта и технического обслуживания. При этом статистический анализ повреждений выявил закономерность их возникновения, что служит важным фактором оценки надежности электрооборудования горных машин. Для количественной характеристики надежности предлагается использовать среднюю ожидаемую наработку до отказа. Этот показатель характеризует относительную безотказность электрооборудования и является основополагающим параметром его надежности. Полученная математическая модель отказов оборудования с разбиение обслуживаемого оборудования на группы по остаточному техническому ресурсу дает возможность реализовывать гибкие ремонтно-обслуживающие циклы. Пример оптимизация системы обслуживания электротехнического оборудования горных машина по уровню надежности - вероятности безотказной работы, выполненной с помощью данной модели показан на рисунке ниже.
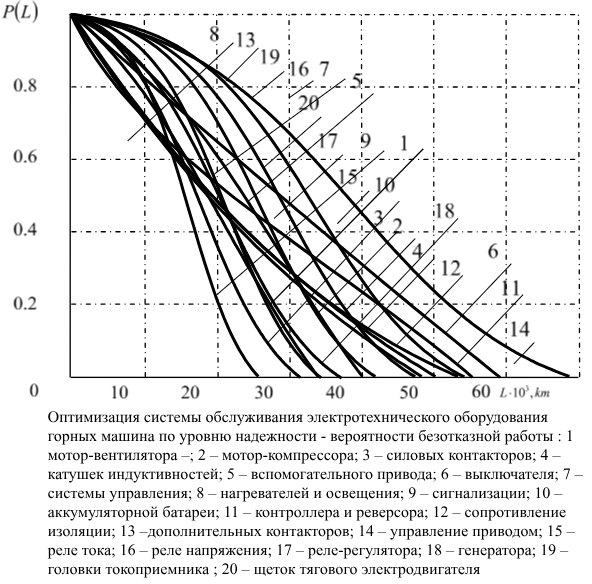
Использование таких циклов позволяет осуществить переход от плановой ремонтной системы к ремонтам по потребности, исходя из технического состояния оборудования.
Заключение. Разработанная в статье модель определения надежности учитывает наиболее и наименее вероятные нагрузки, воздействующие на оборудование в процессе эксплуатации и приводящие к снижению его надежности. Объединяя электрооборудование в группы с примерно одинаковым остаточным ресурсом, можно оптимизировать циклы технического обслуживания и ремонта (ТО и ТР), подобно тому, как это делается в существующих системах, например, в планово-предупредительных системах ремонта. В предлагаемой модели ТО и ТР выполняются по потребности или в зависимости от технического состояния оборудования. С помощью статистического анализа определена вероятность повреждения элементов электрооборудования, которая является важным параметром для оценки надежности электротехнических систем горных машин. В качестве количественной характеристики статистических рядов отказов предлагается использовать математическое ожидание пробега. Относительная характеристика безотказности электрооборудования оценивается как основная составляющая его надежности. Она определяется через показатель, характеризующий количество отказов оборудования на единицу пробега, то есть через интенсивность отказов.